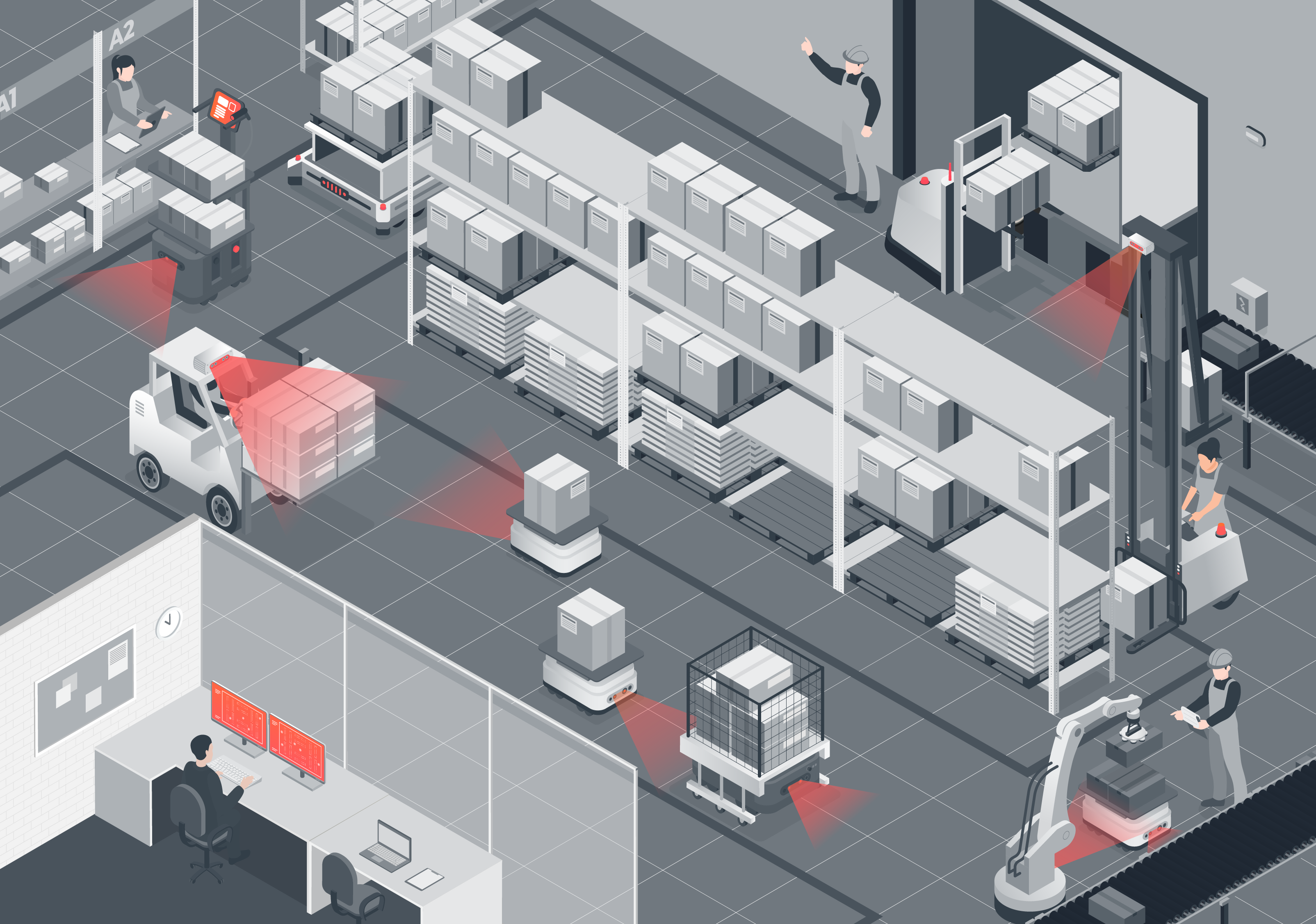
The intralogistics industry has a guilty secret: for much of the time, factory and warehouse operators have no reliable way of knowing where their key intralogistics assets are. Tracking the real-time location of material handling equipment, from forklifts to tuggers and from manually driven vehicles to autonomous mobile robots, is error-prone and inefficient. This creates huge inefficiencies, reducing throughput and hitting the bottom line.
AI is Only as Good as the Data it Receives
Most warehouses and factories are equipped with intralogistics or fleet management systems to orchestrate the flow of goods across the facility. Today, there are increasingly sophisticated orchestration software available that utilize advanced AI to optimize this flow of goods. But to function, they rely on the input of accurate location data from two sources; the vehicles (both manual and autonomous) they seek to direct, and the actual goods and materials that need to be moved.
The problem is, orchestration software assumes that the location data it receives are always correct: but in reality, this is far from the case. Three hurdles currently limit the ability of centralized orchestration software to deliver optimal results:
- The first is that the picture itself is incomplete. Many manually driven vehicles do not routinely and automatically provide real-time location information. The allocation of work is quite often done without actually knowing which operators are best positioned to carry it out.
- Secondly, most autonomous vehicles tend to operate in spatial silos, calculating their own position using external infrastructure or onboard sensors that are subject to their own strengths and weaknesses:
- LIDAR does not cope well around moving objects or in changeable environments and does not produce maps that can readily be shared with other products unless they mount the LIDAR at exactly the same height and orientation
- Magnetic tape is reliable, but rigid and inflexible
- UWB is good in large open spaces but requires expensive fixed infrastructure and suffers from blind spots when things get cluttered
- Finally, most surprisingly, even with all the technical advances, the location of stock is still nearly entirely calculated using ancient technology such as RFID and barcodes that require manual scanning at close proximity.
The result of all of this is that we do not have a reliable view of where everything is in a factory or on a site. This limits the ability to deliver effective intralogistics, planning, and orchestration at the speed and scale required in today’s facilities. There is no common language of spatial intelligence in the ‘mixed economy’ of manual vehicles, autonomous guided vehicles (AGVs), and AMRs, not to mention people, operating in warehouse and factory environments. As a result, speed, safety, and throughput are not optimized: the wheel is constantly reinvented, and efficiency, productivity, and profitability are all compromised.
The problem of inaccurate and patchy asset location data is not going to be solved by every company trying to build and implement their own localization system. On the other hand, it is not going to be solved by a single technology or homogenous positioning solution. The options available today are not necessarily bad, they could just be a lot better.
The Solution is Plain to See
Visual sensors are the key to solving this problem. Vision based localization (VBL) is a technical approach to positioning assets using sophisticated AI to process the data from cameras mounted on moving vehicles. The images are converted into a real-time position of the moving vehicles reliably providing centimeter-accurate location information, 24 hours a day. VBL can act as a primary system for vehicles that have no way of positioning themselves, or as a complimentary localization system for those that do.
However, the real value of using VBL across the factory or warehouse is that it allows vehicles not only to report their own location in a standard, shareable way but also the location of everything their cameras see. This includes other vehicles, people, stock, and even obstacles and spillages. Suddenly not only is the reliability of location reporting of every vehicle improved, but the location of every vehicle and mobile machine is captured in real-time across the entire site.
A Living, Shared, Accurate Map
But is this level of detail important? After all, factories and warehouses seem to do just fine without knowing where their assets are a lot of the time. But, as costs and demands rise, and operators strive to do more with less, the answer is an emphatic yes! Optimization is the key to increasing the throughput of a factory or warehouse and spatial data is critical to optimize operations.
Imagine turning every mobile asset into an information-gathering instrument that contributes to a centralized, queryable map of your facility. Instead of static data collected sporadically and manually using barcode scanners or similar ‘legacy’ technology, operators can see the location of any stock, machine, or vehicle on a dynamic map updated by every camera-equipped machine in real time. Every time a palette or rack is passed by a vehicle, AGV, or AMR (or even a person wearing a bodycam) the position of that object is confirmed and/or updated on the map. Immediately all machines and people with access to that map know the object’s current position and can make decisions confident that the location information they see is true, up to date, and complete.
Vision Based Localization Platform
Visual spatial intelligence represents a platform approach to cracking the issues of reliability and accuracy in large-scale intralogistics environments. Site owners and operators are the ultimate beneficiaries of this game-changing technology, but they can’t just expect third-party suppliers or integrators to offer a complete solution for them. For this to work in practice, it needs to be driven from the top down. It makes sense for the owners and operators of warehouse and industrial sites to drive the adoption of Visual Based Localization by taking a platform approach. Instead of accepting companies providing their own bespoke, localization approaches or installing localization infrastructure that only services a fraction of the requirements, there is a strong argument for sites providing a centralized Vision Based Localization Platform (VBLP) that all moving vehicles can benefit from, whether autonomous or not.
Individual suppliers, rather than reinventing how to localize in each environment or struggling to master endless ‘edge cases’ that cause their solutions to fail, can focus on delivering value to the overall operation. If the ‘what’ and ‘where’ issues are solved by the platform, individual vendors can focus on the ‘why’ – the additional value they can bring to the overall operation. By establishing a consistent way for any intralogistics vehicle to localize itself in that environment, owners will create a platform for faster, effective, at-scale deployments. They will also broaden their range of options for automation suppliers. What’s more, adding cameras to existing intralogistics fleets, or even making additional use of cameras already present, is a relatively low-cost investment with a rapid and significant return.
A Radical Proposal
It may seem a radical step to propose that facility owners invest in creating a VBLP, but it has clear precedents. Vendors of any electrical equipment know that it must operate at a certain voltage and current and connect with standardized interfaces (plugs and sockets) to be acceptable. Vendors are not expected to figure out how to get power to their machines, and site owners are not expected to provide non-standard power solutions. Similarly, the provision of Wi-Fi internet connectivity, conforming to standardized modes of connectivity by site operators, provided the foundation for many of the autonomous, connected devices already dramatically improving productivity in those sites. Just as warehouse owners invest in the provision of electrical and Wi-Fi connectivity across their sites it makes sense for them to take responsibility for a centralized spatial database that allows intralogistics solutions from any vendor to use a common language to communicate with RTLS and logistics management software.
Investing in a VBLP as a central resource means that in the future, any intralogistics innovator, robotics startup, or systems integrator doing business with the site can accelerate proofs of concept by accessing the central database for position data and shorten time to cost-effective deployment.
Just as the early adopters of standardized electrical power got a head start on their competition in the early twentieth century, warehouse owners that take the bold step of providing a centralized Vision Based Localization Platform will be best placed to benefit from the new age of interoperable, efficient and cost-effective large-scale intralogistics management in their factories and warehouses.