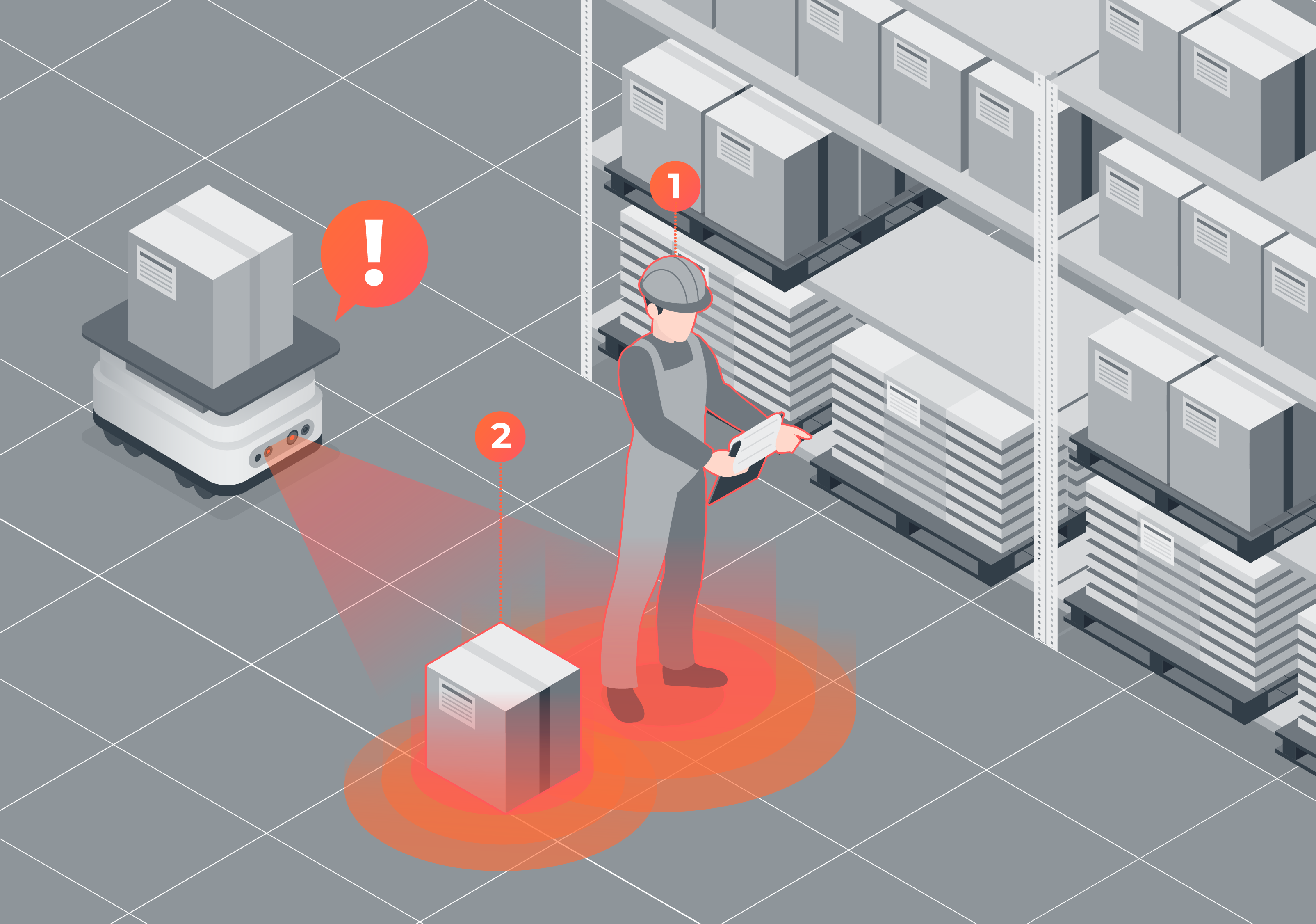
Increasingly, warehouse operators are looking to automate their operations. While many look to LiDAR, UWB, or other sensors – using vision (low-cost cameras and an IMU) to augment localization and mapping for AMRs and manually piloted vehicles adds new capabilities, enhanced safety, and improved efficiency.
Working with leading OEMs of AMRs to rapidly realize the benefits of vision-based spatial intelligence, Slamcore has identified three reasons to consider vision as part of any material handling operation.
ROI is everything
Adding vision to complement existing localization and mapping modalities is a cost-effective solution that can have a rapid return on investment. In many situations, the cameras needed are already being used to identify fiducial beacons, barcodes, or markers in warehouse and logistics facilities. Often playing important roles in improving overall performance.
Slamcore’s SDK simply takes visual feeds from those same cameras and uses them to gather the data that enables full-stack Spatial Intelligence and semantic labeling. Thanks to the efficiency of Slamcore’s Spatial Intelligence SDK, these vision-based capabilities run ‘at the edge’ in real time on even the lowest-power and lowest-cost processors. Regardless of the OEM’s choice of hardware and sensors, Slamcore’s algorithms can reliably deliver Spatial Intelligence when the AMR needs it most.
Rich complement
In practice, Slamcore provides a richness of data to the technologies already widely deployed in a distribution center that only Vision can provide. LIDAR, for example, provides highly accurate localization but, combined with vision, can deliver rich 3D maps of the environment rather than the 2D slices produced by standard LIDAR alone. Not only does this assist with navigation and path planning, but delivers detailed visual representations of the whole view, which can be shared and understood by human operators as well as other devices.
Camera-based visual-spatial intelligence has a wide field of view and can deliver very detailed volumetric maps that aid in rapid path planning and obstacle avoidance. No infrastructure changes are required, unlike other modalities, which require fiducials, tracks, beacons, or other signage to be added to ‘mark-out’ routes.
Facilities need not be closed whilst robots ‘re-map’ the environment after any physical changes to the layout. Autonomous machines equipped with visual-spatial intelligence can create maps as they move and thus respond and instantly share changes to the layout without the need to re-map – increasingly vital to efficient operations in constantly evolving warehouse space.
Perception Increases Efficiency
Perhaps the biggest advantage of vision-based spatial intelligence is the ability to recognize what the objects around a robot are.
Whilst other Simultaneous Localization and Mapping (SLAM) technologies can accurately map objects around them, they cannot define what those objects are. This means that all obstacles must be treated the same, whether they are permanent structures or temporary obstructions, people, or other machines. The feature-rich information captured by cameras allows AMRs to identify different objects in real-time – allowing the robot to make different decisions as to what is and isn’t a safe space to move to.
For example, AMRs with Slamcore designed-in can recognize humans and therefore slow, stop, or navigate around a wide exclusion zone – ensuring there is less chance of an accident. Identifying an obstacle as a pallet or rack, the robot can safely maintain speed and pass closer to these objects, which poses less of a safety risk.
Slamcore’s Spatial Intelligence also has the ability to add permanent or semi-permanent objects to a shared map to benefit other robots and machines. Whether people or other moving objects, vehicles, or robots – AMRs and manually operated machines can benefit from increased awareness of their environment.
Exponential Increase in Value
Throughput and efficiency are at the heart of autonomous operations in intralogistics. Adding vision can aid this by reducing the ‘start-stop’ of robots encountering new obstacles. Utilizing the cameras already added to an increasing number of devices in warehouses and logistics, or even adding low-cost cameras to those that do not have them, significantly enhances the information gathered.
With Slamcore’s Spatial Intelligence SDK, this visual data can be rapidly, accurately, and robustly processed to deliver new capabilities, value, and efficiency to the fast-moving warehouse operation.
If you’d like to learn more, take a look at our eBook Envisioning Efficiency: Revolutionizing Warehousing and Automation with Vision.
Ends
🤖Read more at blog.slamcore.com