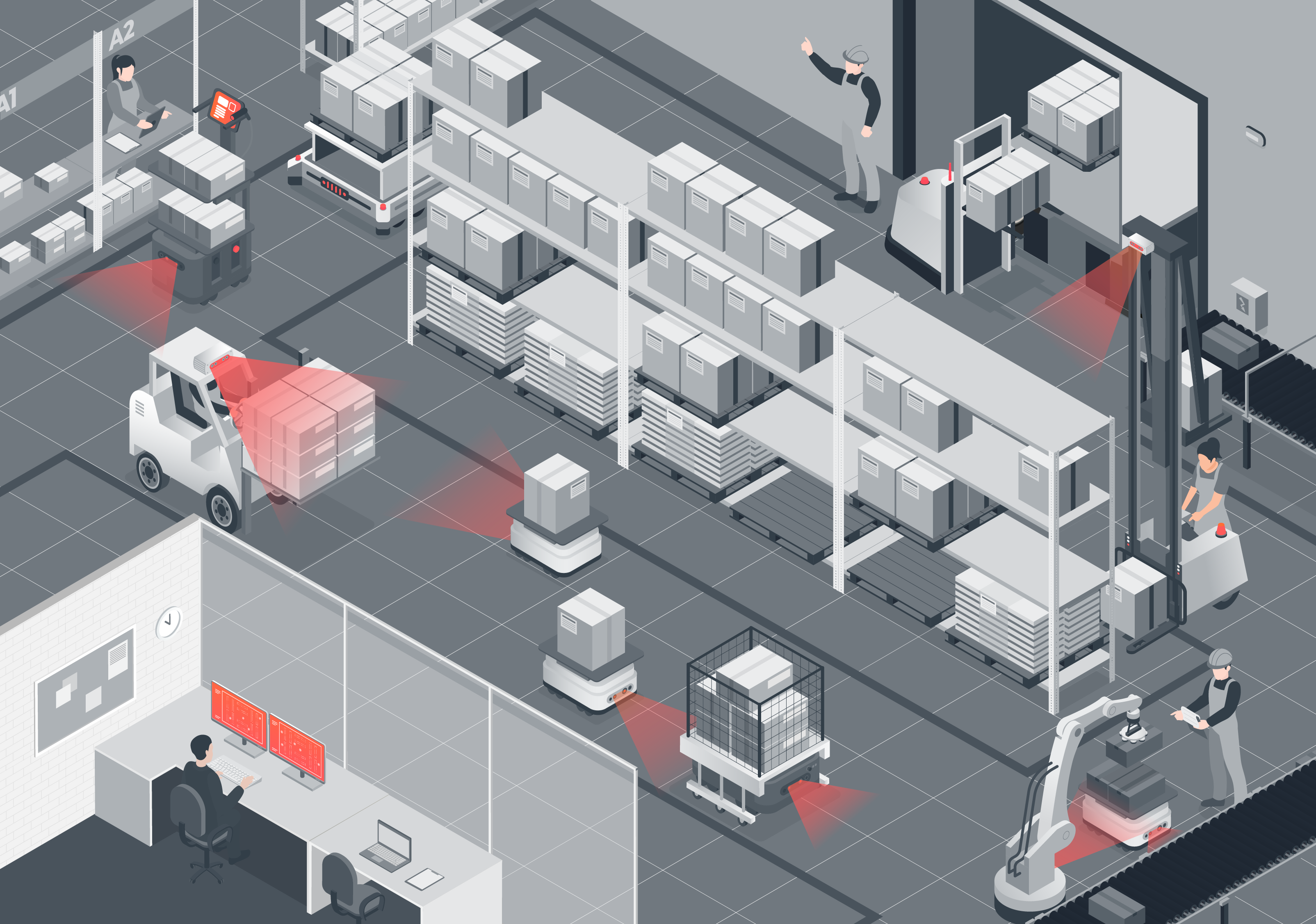
Throughput is everything for today’s factory and warehouse operators. Increasing the speed at which goods safely move through the facility whilst decreasing the cost of physical infrastructure required to move these goods will result in higher profit margins. This simple equation has justified investments of millions in orchestration software and intralogistics management solutions. But, these investments may not be generating the maximum returns. As argued in this blog, they assume the location data they consume is accurate, when oftentimes it is far from it. Without accurate data, intralogistics cannot be optimized. Put another way, conservative modeling suggests that throughput can be increased safely by well over 20% by simply improving the accuracy, reliability, and completeness of real-time location data.
Whatever intralogistics management solutions you use, here are five reasons to improve the accuracy, reliability, and comprehensiveness of your Real-Time Location System and the spatial data it provides.
- Continuous improvement with real-world data
Designing the layout of a factory or warehouse to optimize operations is a complex challenge that requires a sophisticated understanding of the facility, the type of work undertaken, and a wide range of external factors. Today’s consultants and in-house experts devise detailed models that predict routes, layouts, and throughput before a single rack has been positioned. Yet, optimization to maximize throughput remains somewhat a dark art – without accurate data it’s impossible to know how close to optimal your operations really are.
Accurate RTLS data, provides real-time information on every vehicle, autonomous machine, and even person as they move around the facility. Unforeseen bottlenecks can be quickly identified and the root cause established. Operators see in real-time where vehicles are forced to slow down, navigate congestion, or wait to pass junctions, and act to mitigate the situation. You’ll be able to see how and why your most expensive vehicle is traveling far further each day than anticipated, and react to instantly reduce costs. By measuring actual performance against modeled expectations operators can continuously improve efficiency.
- Learn from the mistakes you don’t make
With accurate RTLS data detailed, a shared map of the real-world flows of machinery, goods, and people can be established over time. We can then start to analyze and troubleshoot based on real-time data, i.e. Was that route slow due to other vehicles or because of a spillage? What are the factors that are consistently contributing to specific vehicles taking non-optimal routes? Are there unforeseen problems with the placement of a rack that makes a turn hard to negotiate, or is a more direct route avoided because of congestion? Are there specific areas that lead to more AMR localization failures?
With enough location data over time, it will be possible to track the sequence of events that led to these issues. The real power comes when this historical data is used to monitor the real-time spatial state of the site and intervene if early signs suggest you are en route to an issue, something can be done about it before it happens.
- For the good of the many
There are multiple routes to get from A to B, but there is only one that is optimal. But, what is optimal for an individual vehicle, may not be best for the fleet. A vehicle in isolation may choose a route that it considers the shortest, but this may not actually be optimal for the overall site. Vehicles must operate around many other vehicles and people and will need to modify their routes and speed as they encounter these obstacles.
Accurate RTLS data supports complex route planning at a site-wide level. Rather than simply selecting the best route for an individual vehicle, real-time data showing the location of all assets enables optimization of all routes. Moreover, when combined with historical data, it can predict where everything will be in the future. So the optimal route for one vehicle can be planned without interrupting the best route for any other.
- Human drivers included
With the drive to automation and autonomous operations, it is easy to forget that in most facilities manually driven vehicles still make up the majority of assets. These are expensive machines, even more so when you include the cost of the staff operating them. So, it is essential that these machines are also used optimally. Having forklifts sitting around waiting for jobs or tuggers being driven along inefficient routes is a huge waste of money.
Adding sensors (especially low-cost cameras with visual AI algorithms and processors) equips these assets to report on their position and that of objects, other vehicles, people, and infrastructure around them. All of which contributes to more accurate RTLS that ensures better utilization, more efficient routes, and reduced downtime from these expensive assets.
- Speed and Safety
With more vehicles and humans operating together, the risks of serious accidents can increase. Knowing where everything is, all the time, provides a new level of situational awareness that drastically reduces the potential for accidents. As discussed in this previous blog, with modern day RTLS systems that use cameras to calculate their position, vehicles can accurately report not only their exact position but also the position of everything they ‘see’ around them. This means that the quality and quantity of information available to everyone on site is dramatically increased.
Pedestrians as well as vehicles can be warned of hazards that are beyond line of sight. Individuals can be equipped with body-worn cameras that report their position as well as the position of vehicles they observe, contributing to a real-time map of the entire facility. Clearly, there are privacy and ethical considerations related to tracking individuals, but the benefits of being able to identify people and share their location with the entire fleet allowing routes to be updated or speeds changed to improve safety are hard to disagree with.
Ultimately, all of these benefits contribute to more efficient operations. The closer to optimal intralogistics movements are, the faster throughput can be achieved safely. Accurate RTLS data is the key to getting value from investments in logistics management, and ultimately will have a huge impact on the bottom line increasing operating profits by millions of dollars a year.
Get in touch to find out how Slamcore’s visual spatial intelligence can be simply added to any intralogistics environment to provide rich, accurate, and real-time data to improve any RTLS.
Or come and discover the latest Slamcore 3D visual positioning products at Modex 2024 from March 11-14 in Atlanta, Georgia, we will be in Hall A Booth A13918. Book a meeting with us to explore how Slamcore AI-powered products enable the next generation of intralogistics solutions.